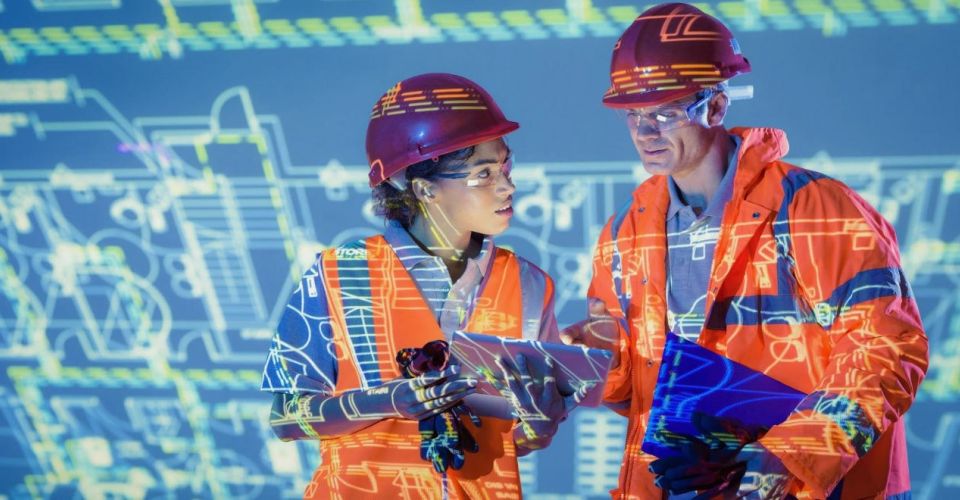
Prepared by Doug Kibler, Affine Consulting
Introduction
Asset-intensive organizations across multiple segments such as energy, public sector, manufacturing, transportation, pharmaceutical and more have invested millions of dollars in systems from Enterprise Resource Planning (ERP), Enterprise Asset Management (EAM), Scheduling platforms, and as of late, Work Execution platforms. Investments were made to help address market pressures to reduce operating costs and improve reliability, and safety.
PLANNING IS CRITICAL "In preparing for battle, I have always found that plans are useless, but planning is indispensable." General Dwight D. Eisenhower
Is it possible that even with these sizeable investments negative trends will still be present preventing the delivery of the desired return-on-investments for capital projects, shutdown and turnarounds, and plant operations?
The truth is many variables exist that can drive negative trends to include frequent downtimes and emergencies (or the ability of the asset to meet its designed function when required), scope creep, unavailable materials and the correct resources, disorganized maintenance to include the inability to create an inefficient schedule for work execution and supporting systems.
These negative trends can be driven from an undefined asset management framework starting with the lack of an Asset Management Policy, Strategic Asset Management Plan, Asset Management Plans and supporting processes to include for asset acquisition, operation, maintenance, and disposal. Systems supporting these processes can be disjointed, found to be lacking in the functionality needed to optimize the desired processes, or improperly implemented.
In many cases, the issues are driven from a lack in maturity in capital project and maintenance job planning affecting all downstream processes performed in both asset on-line and outage and turnaround conditions. Today, capital project and maintenance job planning has gained more significance due to the digital transformation sweeping across asset intensive industries over recent years. It has now become crucial for ensuring a competitive advantage is achieved or maintained and meeting their defined mission and vision.
COMPLETE AND CLEAR JOB PLANS Field technicians should be able to complete their assigned work without having to stop to research new data. Permits, documentation, materials, and in some cases job history should be available for efficient execution of work. Solutions with Field Tablets enabling workers with critical data are fueling digital transformation in the planning industry.
This white paper addresses the key function of capital project and maintenance job planning; a key role in ensuring organizations can schedule and perform cost-effective maintenance driving improved asset performance, reducing emergency repairs and unplanned downtimes. It also discusses barriers to efficient work performance driven by planning as well as solutions to address identified gaps.
The recommendations in this paper are linked to my career in the Navy’s Nuclear Program, working in and leading planning and scheduling departments at commercial nuclear power plants and other energy industries, product management for software solutions, and asset management consulting.
What is Capital Project and Maintenance Job Planning?
Planning both capital projects and maintenance job plans are critical to the efficient and safe execution of work. Maintenance planning defines the “what, why and how” and when the work should be performed. The schedule determines the “when and by who”. Both must integrate to achieve the desired efficiency.
Plans cover work to be performed while facilities are in an operational state as well as when they are required to be shut down in order to safely perform the planned work. They can cover key processes such as scope definition, work requests and work order management, and lead to the creation of plans detailed to a level required based upon the asset classification and criticality for the safe and efficient execution of work. It can also include work performed within the scope of a capital project that can be done in either (or both) in a shutdown or online state.
Planning allows for the addressing of future tasks from the backlog to determine work details, skills required, budget and time required to perform as well as other supporting requirements.
These can include:
- providing procedures, vendor manuals, and equipment
- system drawings, required consumables and spare parts
- providing detailed work instructions
- establishing required commercial contracts
- defining required quality assurance and quality control steps
This level of planning greatly improves work safety and efficiency and ‘wrench time’ of field technicians.
Further improving efficiency is the ability to document work plans and provide direct field feedback whilst the digital transformation is underway.
Defining the Process
Processes are developed by asset classification as defined within the Strategic Asset Management Plan and the processes developed in support of the Asset Management Plan for asset creation, operation, maintenance, and disposal.
Defining the maintenance planning process is an important aspect used in conjunction with determining the required planning functionality and configuration from your selected EAM or CMMS.
This ensures consistency in measuring key performance indicators for process optimization and provides a baseline for continuous process improvement.
Impacts of Asset Management Systems
Organizations have invested millions of dollars in many cases in the selection, implementation and operation of enterprise asset management systems or computerized maintenance management systems. These systems address at different levels the maintaining of equipment assets through the performance of corrective to preventive or predictive maintenance actions. With the addition of the Internet of Things (IoT), direct integration of predictive technologies such as vibration analysis is directly monitored by these applications to predict potential failures before they happen.
Implemented EAM / CMMS Systems are expensive investments and cannot be replaced to optimize focused planning processes. Solutions are required to allow for improved planning capabilities while retaining existing system investments.
While they can perform and analyze more than ever before, limitations are found in the ability to adequately perform and report planning status required by internal enterprise processes and policies.
Addressing the Gaps in Planning Capabilities
Middleware planning solutions are relatively new as compared to the traditional CMMS planning capabilities. They are designed for ease of use, mobile capabilities, and visibility and management of the job planning process in support of both online and shutdown, turnarounds, and outage work. Most importantly, existing CMMS and EAM solutions do not need to be replaced and are optimized by these solutions’ extensive planner-focused capabilities.
The better the quality of the work order plan, the higher is the probability of success in the scheduling and execution of the project.
Additionally, these focused planning solutions (such as IAM Tech’s iPlan STO, Maintenance, and Ultimate product offerings) allow for the contract planner and controls personnel to modify work orders without access to critical IT applications. Expensive training, software licenses, and ongoing support are removed providing improved efficiency without compromising internal staff workload. Systems allow executive stakeholders, turnaround, maintenance leadership, planning managers and planners to perform activities not found in typical EAM and CMMS solutions to include:
- Allowing for the planning execution of your STO event using historical data and defined workflows greatly reduces the plan development time and effort.
- Increased security to ERP systems by offering access to required planning information to contractors and owners alike without the risk of compromising the source data.
- Provide a single planning system consolidating data from multiple disparate sources for efficient planning processes.
- Support remote planning capability greatly reducing risks imposed by the COVID-19 pandemic.
- Improve efficiencies in scope development and scope change management to include risk analysis and integration with Primavera.
- The normal and schedules of rates within the STO enable rapid estimation of turnaround and outages.
- Support permitting to include hot work, electrical isolation, mechanical isolation, blinds, and others.
These capabilities, along with others, will greatly improve planning efficiencies and visibility, improving equipment uptime and reliability, and ultimately, increasing the financial performance of the implementing organization.
Managing equipment assets is critical to successful business outcomes as it can improve decision-making, mitigate risk and reduce the total cost of ownership. Our offerings described below include an 'AS-IS' Baseline Engineering Study, Creating the Asset Management Framework, Policy, and Strategic Asset Management Plan, and addressing the Asset Management Infrastructure.
Conclusion
Optimizing maintenance planning for STOs, Capital Projects, and/or Maintenance is critical to the financial wellbeing of asset-intensive organizations. With gaps in traditional ERP, EAM, and CMMS solutions ability to meet planning demands, new approaches must be identified and implemented.
It is a worthwhile investment for your organization to look at what efficiencies can be made possible with the latest technologies in capital project and maintenance management planning.
About the author
Doug Kibler is a Solution Principal at Affine Consulting and and acts as North America Representative for IAMTech
www.affineconsulting.com
info@affineconsulting.com
Office: 985-239-5623