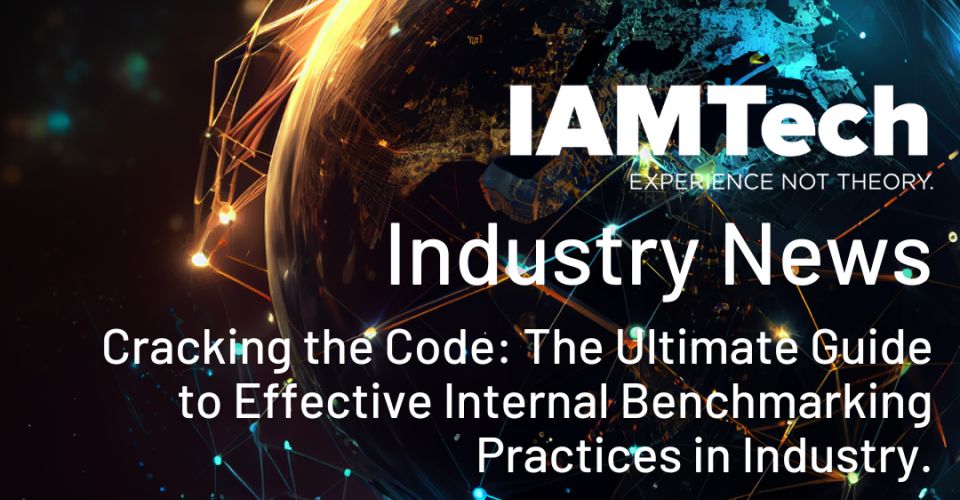
Introduction:
In an era where efficiency and performance are at the forefront of business success, internal benchmarking emerges as a pivotal tool for industrial organisations. This practice, distinct from external benchmarking, concentrates on evaluating and comparing processes within a company, offering a unique perspective for pinpointing improvement areas. Internal benchmarking, whether employed as a precursor to or in place of comparing against external competitors, serves as a vital strategy. It enables organisations to refine their internal processes, potentially creating a robust foundation that can evolve into a key competitive edge.
Opting for internal benchmarking often proves more resource-efficient, both in terms of time and financial investment. Unlike external benchmarking, which demands access to often elusive or expensive competitor data and insights, internal benchmarking focusses on your organisation's own processes. This introspective approach facilitates the identification of best practices, highlights inefficiencies, and uncovers areas ripe for enhancement. With a thorough understanding of your internal workings, you can craft targeted improvement plans that are finely tuned to your company's specific challenges and opportunities. Moreover, internal benchmarking negates the need to divulge sensitive internal data or seek confidential information about competitors, thus sidestepping potential ethical or legal pitfalls.
By embracing and adeptly implementing internal benchmarking strategies, companies can not only enhance their processes but also foster a culture of continual growth and learning.
Understanding Internal Benchmarking:
Internal benchmarking involves comparing internal processes and performance metrics within the same organisation. Unlike external benchmarking, which looks outward to compare with other companies, internal benchmarking offers a more introspective view.
This practice is essential for identifying the 'best of the best' within an organisation and leveraging those insights to elevate overall performance. For example, during a plant(s) STO (Shutdown, Turnaround or Outage) software such as iPlanSTO can help you compare estimate vs actual, for a single activity, work order, or across an entire trade, to optimise future STO performance. iPlanSTO retains all historical Shutdown - Turnaround - Outage, work order & work package data.
This history can be re-utilised time and again so that users can understand all historical works, estimated effort & costs, versus, actual effort & costs, & ability to capture lessons learned when completing works: improving accuracy of future planning! The benefits are clear: accurate forecasting of future labour effort, greater confidence in plant downtime windows, cost reductions, and the fostering of a performance-driven culture.
“If you never look down while you’re climbing the ladder you won’t know how far you’ve come” – Unknown
Step-by-Step Guide to Effective Internal Benchmarking:
- Identifying Benchmarking Objectives: Begin with clear, measurable goals. What do you want to achieve? Is it process efficiency? cost reduction? employee productivity? or customer satisfaction? Clear objectives guide the entire benchmarking process and ensure that efforts are aligned with your organisational goals.
- Choosing Benchmarking Subjects: Once objectives are set, select key processes or performance metrics that align with your objectives and identify which departments, processes, or operations will be the focus of your benchmarking. This could range from manufacturing processes to HR practices.
- Data Collection and Analysis: Data is the cornerstone of any benchmarking process. Collect comprehensive data on the chosen subjects, focusing on metrics that directly relate to your objectives. This data must then be analysed to identify performance gaps and areas of excellence. Advanced analytics tools and software, in particular business intelligence platforms, such as PowerBI, can be particularly useful in this stage, offering deeper insights and predictive capabilities. Utilise both qualitative and quantitative methods for a holistic view.
- Learning from Best Practices: Investigate the top-performing teams, areas or functions. What are they doing differently? How can these practices be adapted and implemented in other areas of the organisation? This phase often involves cross-departmental collaboration, breaking down silos to share knowledge and strategies.
- Implementing Improvements: Develop a plan to apply the best practices identified. This should be approached systematically, with clear plans and timelines, and most importantly action owners for each improvement, making the person accountable to deliver the improvement by a mutually agreed milestone. This might involve training, process changes, or resource reallocation.
- Monitoring Progress: It's equally important to monitor the impact of these changes, adjusting strategies as necessary to ensure they deliver the desired outcomes. Establish metrics to track the impact of changes. Continuous monitoring allows for adjustments and ensures long-term success.
Common Challenges and Solutions:
Internal benchmarking is not without its challenges. Resistance to change is common, employees may be sceptical or apprehensive about adopting new practices and departments may be protective of their methods.
Overcoming this requires strong leadership and a culture that values continuous improvement and learning. Ensure transparent communication and involve teams in the process.
Data integrity can also be an issue. To mitigate this, use robust data collection and validation methods.
Lastly, navigate internal politics by fostering an environment of collaboration, not competition.
The Role of Technology:
Technology plays a pivotal role in modern benchmarking practices. From data collection tools to analytics software, technology can streamline the benchmarking process, enhance accuracy, and provide actionable insights more efficiently.
This is particularly true in the industrial sector, where we've seen the benefits of software tools like iPlanSTO for internal STO business process benchmarking, providing data to help attain the insights.
Additionally, embracing technologies such as the Internet of Things (IoT) and Artificial Intelligence (AI) offers the advantage of real-time data and predictive analytics, transforming benchmarking into a more proactive and future-focused practice.
Conclusion:
Internal benchmarking is more than a process improvement tool; it's a catalyst for organisational transformation. By embracing these practices, businesses can not only optimise their current operations but also pave the way for sustained innovation and growth.
While external benchmarking is valuable for understanding your position in the market and identifying industry best practices, starting with internal benchmarking ensures that you are making the most of your internal resources and capabilities before looking outward. It's often a strategic first step in a broader benchmarking and improvement process.
Internal benchmarking is not just a process of comparison; it's a strategy for continuous improvement. By systematically identifying and leveraging internal best practices, companies can enhance their performance in a focused, efficient manner.
Please remember, the goal of benchmarking is not to emulate but to evolve – to take what's working and adapt it in ways that drive your organisation forward. In the fast-paced industrial world, internal benchmarking is not just a tool for success; it's a necessity for survival and growth.
Call to Action: We invite you to share your experiences with internal benchmarking or suggest topics for future insights. Your engagement helps us all grow together.