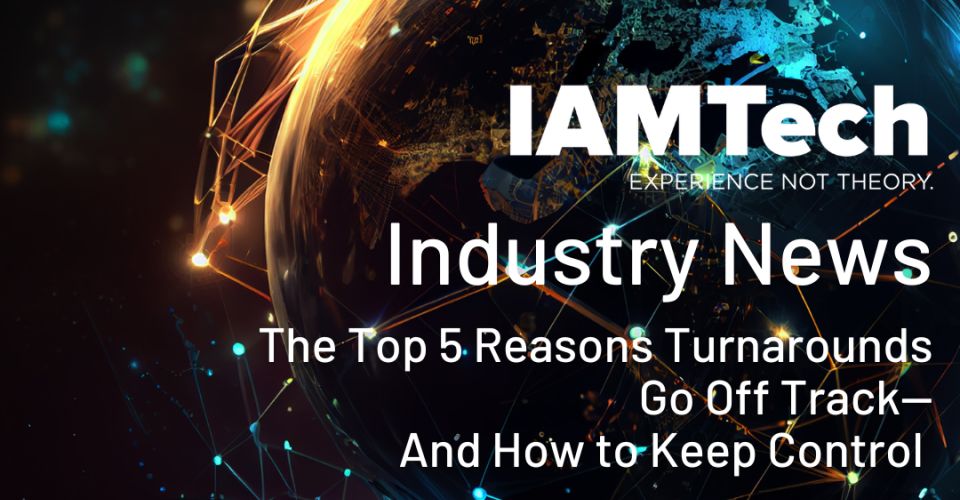
A plant turnaround is a planned, periodic shutdown (total or partial) of a process unit or an entire plant to perform essential maintenance, overhauls, inspections, or replacements and can often be as a result of regulatory compliance. Turnarounds are critical to a plant’s operational health, reliability, and profitability. However, the complex nature of these events can lead to safety incidents, significant cost overruns, and production delays when poorly managed.
Industry research reveals that 80% of turnarounds exceed their budgets by at least 10%, and 82% do not meet performance expectations, highlighting the challenges faced by plant operators.
Below, we examine the five most common reasons why turnarounds fail and how to mitigate these issues.
1. Inadequate Planning and Control
One of the most significant causes of turnaround failure is poor upfront planning. Insufficient planning often results in cost overruns, schedule delays, and operational inefficiencies. Research shows that 80% of turnarounds experience cost overruns, often due to a lack of detailed planning and misaligned resource allocation.
To avoid these pitfalls, companies should ideally begin planning 12-18 months in advance, carefully defining the scope of the turnaround, establishing a detailed schedule, and ensuring that all necessary resources and materials are in place before the shutdown begins. The success of the planning phase is crucial, as it sets the foundation for the entire event.
2. Scope Changes ‘Scope Creep’ and Incomplete Information
Scope creep is another frequent issue during turnarounds, where the original turnaround scope expands due to unforeseen tasks or equipment failures. Typically, c.90% of turnarounds experience scope creep and this can be in the range of 10-50% of total work executed leading to budget overruns and extended event timelines.
One effective strategy to combat scope creep is to ensure clear and robust work inclusion protocols and to use data-driven tools for accurate, real-time tracking of work progress and potential deviation. Digital solutions and predictive maintenance technologies are helping companies identify equipment issues before they escalate, reducing the likelihood of unplanned work and minimising scope deviations.
3. Outdated Tools and Poor Data Management
Many organisations still rely on outdated tracking systems or disjointed data management practices. This can make it difficult to track event progress, forecast costs, and monitor labour productivity in real-time. Less than 20% of turnarounds effectively implement cost control and forecasting, leading to missed deadlines and overspending.
Implementing modern, integrated STO software tools, such as iPlanSTO enables efficient cost control and decision-making. From labour productivity to cost tracking, the iPlanSTO platform offers a wealth of data that enables plant operators to make informed decisions.
This data-driven approach is essential for managing the unpredictability of turnarounds, improving efficiency, and preventing costly delays. One of the most powerful features of iPlanSTO, STO Software is its ability to provide detailed analytics on turnaround performance providing visibility into both equipment status and workforce productivity, improving overall event management, and reducing downtime.
While implementing a software solution may seem like a significant investment, the ROI provided can dwarf the initial investment within the first year of adoption.
4. Poor Communication and Coordination
Turnarounds involve multiple teams, contractors, and suppliers, all of whom must work together seamlessly to ensure the event stays on track. Without proper communication channels and coordination, turnaround events often suffer delays. Approximately 50% of turnarounds face schedule delays due to poor information flow and mismanagement.
Effective turnaround management requires an integrated approach, where the client, contractors, and subcontractors all have access to the same information in real-time. Regular meetings and updates are essential to ensure that everyone remains aligned on goals, progress, and any emerging issues.
Tailored STO Software can facilitate communication and team coordination; with real-time progress tracking and the ability to integrate seamlessly with your P6 schedule coupled with iPlanSTO's S-CURVE, Turnaround Teams are presented with the most up-to-date information for use during their morning meetings rather than relying on outdated information.
This significantly increases the chance of bringing the plant back online and to schedule.
5. Lack of Contractor Integration
The integration of contractors into the overall turnaround organisation is often overlooked, yet it is essential for the event's success. When contractors are not fully integrated, unplanned additions can cost 30-50% more than originally planned work.
To mitigate this risk, companies should build strong relationships with contractors early in the planning phase, ensuring that they are fully aligned with the event’s scope, schedule, and goals. Proper contractor management also involves clearly defining roles, responsibilities, and performance expectations from the outset.
Key Takeaways for Successful Turnarounds:
- Integrated Turnaround Teams: Ensuring close collaboration between the client, contractors, and subcontractors.
- Pre-Execution Control: Invest significant time in detailed scoping and planning.
- Data-Driven Decision Making: Use modern software tools such as iPlanSTO, STO Software for real-time data tracking and event analytics.
- Clear Communication: Maintain open and timely communication across all stakeholders.
- Strict Scope Management: Avoid scope creep by clearly defining the turnaround scope and using predictive tools to anticipate problems.
By addressing these common failure points and implementing best practices, companies can significantly improve their turnaround performance, reduce costs, and enhance plant reliability. Digitalisation, integrated software solutions, and early, meticulous planning are the keys to preventing costly delays and ensuring that turnarounds stay on track.
To learn more about iPlanSTO head over to our website and book your live online demonstration ShutdownTurnaround Outage Software for industry - IAMTech.