Introduction
A Shutdown, Turnaround or Outage (STO) is a complex and extensive process that involves stopping a plant or facility for a set period of time, to perform essential maintenance, repairs, or upgrades. The typical activities and operations involved in an STO event can vary depending on the type of asset, the scope of work, and the duration of the Turnaround.
A successful plant shutdown, turnaround or outage requires careful planning, management, and execution to ensure that the plant or facility is properly prepared for the shutdown process and that all the necessary repairs, replacements, and upgrades are completed on time and within budget.
Anyone in the Turnaround Maintenance planning game knows that a) accurate & b) consistent, task estimation is a challenge. This is then further complicated when calculating the duration, effort & cost of 10000’s of activities for a major event.
Norms based estimation is a method of estimating the effort to perform maintenance activity, calculated using historical data, industry standards & industry activity benchmarking, to generate estimates for activity effort and if resource rates applied, their cost also.
When it comes to STO planning, using norms-based estimation can provide asset owners and their maintenance contractors, several benefits.
In this whitepaper we look at how norms can increase the accuracy of your estimation and refine your estimates, helping you to achieve a plus or minus accuracy of 10% when planning & budgeting for your next STO!
What are norms?
Industry standard norms are commonly accepted and widely used standards or benchmarks within a particular industry. These norms are often developed by industry associations, regulatory bodies, or other organisations with expertise and experience in the industry.
In the context of STO’s, industry standard norms can include guidelines for the duration of shutdown, effort & cost estimates for various activities, safety and environmental standards, and quality standards. These norms are developed by industry associations, regulatory bodies, and experienced organisations.
By using industry standard norms, Turnaround teams can develop more accurate effort & cost estimates, better plan and execute their event, and ensure compliance with safety, environmental, and quality standards. These norms can also be used to benchmark the performance of a plant or event against the industry standard and identify areas for improvement.
Norms datasets are produced by recording and evaluating historical maintenance activities. Maintenance activities are undertaken many times, with their actual durations & number of resources required to perform the activity, is recorded and evaluated to determine a reliable mean effort – the recording and evaluation of these activities produces reliable planning norms, that can then be used to then plan future maintenance activities.
Norms Based Estimation – what is it?
Norms-based estimation is a method of effort & cost estimation, that involves using historical data, industry standards, and benchmarking to develop effort & cost estimates for as many activities in an event as possible. This technique is used to develop accurate effort & cost estimates based on the historical data from similar plant shutdowns, industry standards, and benchmarking.
It involves breaking down the event into activities, estimating the time and resources required for each activity, and then aggregating the estimates to determine the overall manhours & cost of the event.
Historical data and industry standards can be used to determine the time and resources required for each activity, typically norm sets are broken into categories, based on the size and complexity of the asset, the type of equipment and systems, and the type of resources required for the maintenance or repair work to be performed.
Studies show that initial scoping achieves an estimated accuracy of +/– 30%, whilst detailed estimation using norms achieves a +/– accuracy of 20%. Norms + Planning Factors can then increase the estimate to +/- 10% accuracy.
Norms-based estimation can be useful in identifying the potential cost overruns and deviations from the budget during the planning phase. During the execution and lessons learned stages, you can then compare the actual costs incurred during the event with the planned costs. This enables the Turnaround team to identify the areas where cost savings can be made and take necessary actions to avoid similar issues in the future.
Overall, norms-based estimation can help in developing accurate effort & cost estimates, better resource allocation, and cost control during the event. It is a valuable tool for STO planning and management, which can help to ensure that the event is completed on time, within budget, and to the required quality standards.
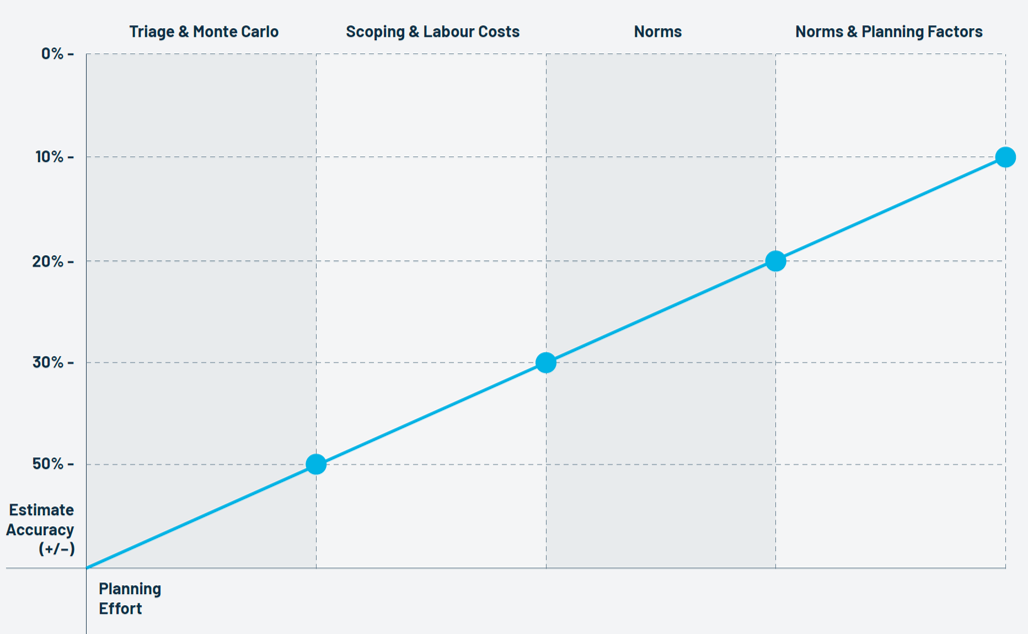
Why is this important?
Estimating the manhours, type & number of resources, overall duration and cost of work order activities is something maintenance planners need to do every day; however, accurate and consistent forecasting is difficult, even for experienced planners.
The importance of norms was demonstrated by IAMTech in 2021 when they conducted an experiment during one of their iPlan training courses.
IAMTech provide a software solution called iPlanSTO, which is a comprehensive suite of software tools that helps organisations scope, plan, schedule and execute their Shutdowns, Turnarounds and Outages more effectively. It is packed with features specifically designed to improve STO processes, including norms-based estimation.
On day 2 of their iPlanSTO training course with a new iPlan client, IAMTech were looking at why norms bring benefit; please see their findings below:
From decades of experience, we have seen how wildly activity estimates can range, even amongst the most experienced of planners and estimators. This is due to the immense complexity and scale of capital projects, and a little-known phenomenon called anchoring, where an individual depends on an initial piece of information to form a decision.
We asked a couple of questions in the breakout rooms using a scientific method, replicating an experiment conducted by Nobel Peace Prize winning social scientist, Daniel Kahneman. The group was split into two teams, and each asked each a baseline question.
Group 1 was asked: Was Gandhi older or younger than 35 when he died? Please guess his age.
Group 2 were asked: Was Gandhi older or younger than 114 when he died? Please guess his age.
Group 1 guessed on average 50 years.
Group 2 guessed on average 81 years.
The actual answer is 78.
What is truly astonishing is the vast difference in the estimated age between the two teams. We asked the teams why they thought there was such a discrepancy. They correctly answered that it was due to the two different anchor questions – was Gandhi older or younger than 35 OR 114 when he died?
Seeing the results, participants concluded that they had gravitated towards the number in the baseline question.
The trainer explained that our brains are very lazy and take shortcuts whenever possible. Instead of trying to work out an answer, our brains will try to match up the information with another piece of information that we know.
This phenomenon is called Anchoring and is a cognitive bias where an individual relies too much on an initial piece of information offered (called the ‘anchor’) to base future decisions and judgments on.
In this case, few of the attendees were likely to have much knowledge about Gandhi, so relied on the one piece of information they were given. This heavily anchored the guesstimate, and whilst the age of 114 was absurd, it did significantly skew the result.
Cognitive bias also happens during STO planning, where we are influenced by useful and perhaps not so useful information, even with the benefit of experience.
Next, the groups were asked to estimate creating and dismantling a simple scaffold structure with the following brief:
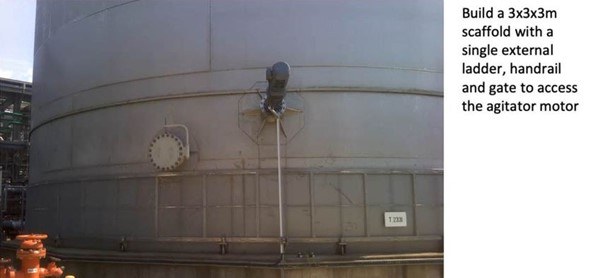
Again, the estimates of effort required for this activity ranged widely, as seen in the graph below:
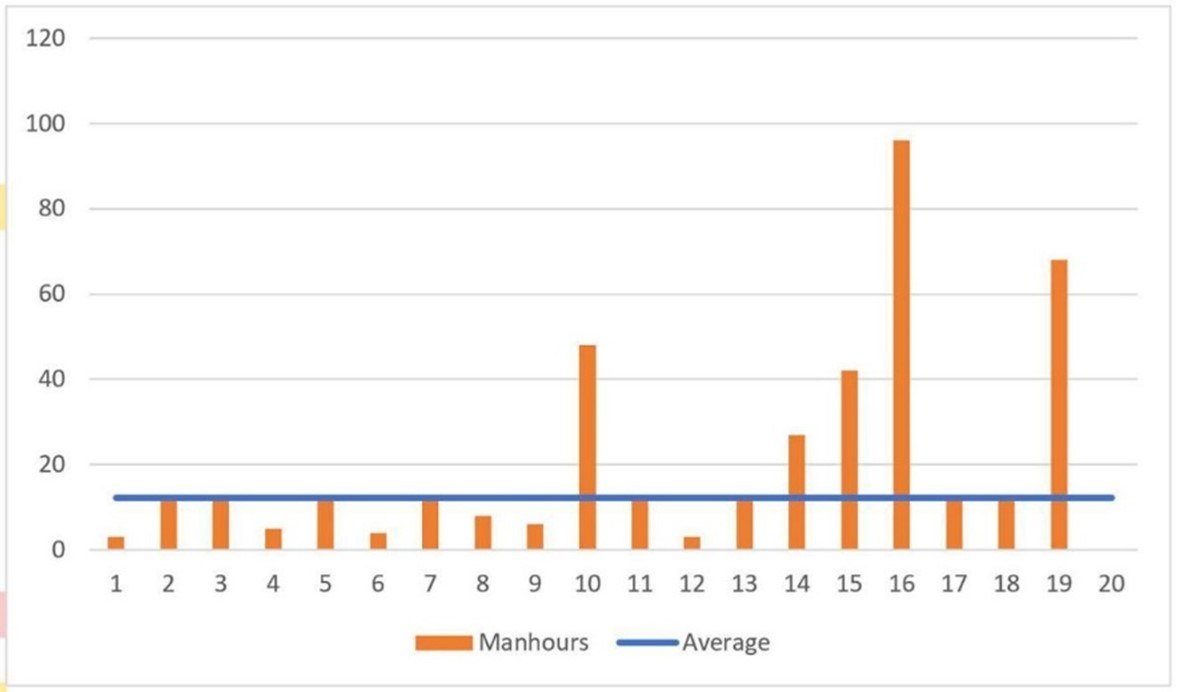
The IAMTech trainers concluded that we must be more data driven when it comes to our estimation.
Norms based estimation removes anchoring, guess work and opinion, which in turn brings standardisation and consistent estimation.
iPlan achieves this by are storing both the planned estimates and the actual activity duration, even after event closure, which can be reviewed and used for new work orders. This saves planning effort and makes the whole process more efficient and cost effective each time the data is assessed to plan future activity.
Crucially, standard estimates can be saved as norms, meaning all staff can benefit from shared knowledge and practices.
The myriad of benefits includes accurate forecasting, ability to compare work orders, ability to compare STO’s, and the confidence to reuse historical work orders, which is how you can save planning effort.
What are the key benefits of using norms-based estimation?
During the planning phase of a plant turnaround or shutdown event, they can help improve cost control, resource allocation, and project planning, and during the execution phase they can aid in better cost control, resource management, event performance and communication, all whilst building the data necessary for continuous improvement:
- Cost Control and Resource Allocation: Norms-based estimation provides a foundation for effective cost control and resource allocation. By using industry norms and historical data, estimators can develop accurate cost estimates, identify potential cost overruns, and allocate resources accordingly. This helps organisations optimise their budgets, prevent cost overages, and ensure efficient use of resources during turnarounds.
- Event Planning and Performance: Norms-based estimation enhances STO planning and performance by providing a reliable baseline for estimating task durations and resource requirements. Planners can use norms to create realistic schedules and allocate resources appropriately. This improves the overall STO planning, reduces the likelihood of schedule delays, and enhances the overall performance of the event.
- Communication and Collaboration: Norms-based estimation promotes effective communication and collaboration among stakeholders involved in plant turnarounds. By using standardised estimation methodologies and industry norms, planners can easily communicate and justify their cost estimates to Turnaround managers, executives, and other stakeholders. This common understanding fosters collaboration, reduces conflicts, and improves decision-making throughout the turnaround process.
- Continuous Improvement: Norms-based estimation facilitates continuous improvement by providing a feedback loop for refining and updating norms based on actual event data. As organisations collect more data from completed turnarounds, they can analyse the variance between estimated and actual costs, durations, and resource utilisation. This analysis enables the identification of improvement areas, adjustments to norms, and the development of more accurate estimation models over time.
Digitised Norms Based Estimation (IAMTech’s iPlanSTO software)
The iPlan software from IAMTech includes norms as standard and if you apply planning factors with norms, then iPlan can help you further refine your estimates to achieve a plus or minus accuracy of 10%. Norms ensure that those estimating the work are using the same estimation methodology agreed between the maintenance provider and the asset owner operator.
iPlan software allows organisations to leverage captured data to refine and update their norms over time. By capturing data from completed turnarounds, organisations can analyse actual event performance, identify areas of improvement, and update their norms accordingly.
With built-in norms templates, you can immediately improve your estimation with the assurance that the norms data is based on real data from hundreds of STO’s. The norms library built into iPlan was first developed 20 years ago and comes preloaded with industry norms, for a variety of activities, such as:
Electrical
Fabrication
Instrumentation
Insulation
Mechanical
Painting
Scaffold
Valve Overhaul
Mechanical Structural Fabric Maintenance
iPlanSTO’s norms library has been refined over the past 2 decades by using the knowledge gained from working closely with each of their clients and are based on millions of maintenance hours and hundreds of STOs.
These norms serve as a starting point for estimation and can be customised as needed. Additionally, users have the flexibility to define custom norms based on their organisation's historical data, specific site conditions, or unique requirements. IAMTech undertake norms review with their new clients as part of the implementation process, to ensure clients get the maximum benefit from this feature.
Conclusion
Norms-based estimation offers significant benefits for STO events. By leveraging industry norms, historical data, and benchmarking, organisations can improve estimation accuracy, achieve cost control, enhance resource allocation, and foster collaboration among stakeholders. iPlan software provides a comprehensive solution for implementing norms-based estimation, allowing organisations to streamline their estimation process, ensure consistency, and leverage real event data for continuous improvement.
With iPlanSTO, users can benefit from preloaded industry norms and the ability to define custom norms tailored to their specific needs. This software enables organisations to generate accurate cost estimates based on historical data and industry benchmarks, leading to more efficient and successful shutdown, turnaround & outage events.
By embracing norms-based estimation and utilising iPlan software, organisations can optimise their STO events, reduce risks of cost overruns and delays, and drive continuous improvement. This approach provides a solid foundation for effective planning and execution, ultimately leading to increased STO efficiency and profitability for the asset owner operator by increasing the likelihood of successfully meeting the plant startup.